固化树脂涂层各项特性的测试设备和测试方法如表2所示。
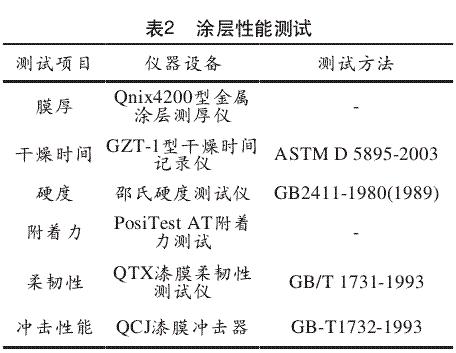
涂层性能测试
2·结果与讨论
2.1 干燥时间
树脂的干燥时间直接影响到涂料的施工性能。本文以D230为固化剂,考察了4种不同环氧树脂的干燥时间,如表3所示。结果表明,混合型环氧树脂由于其含有3个环氧基团,固化速度极快,3小时内即可实干;氢化双酚A环氧树脂固化却非常慢,24h后仍然无法表干。
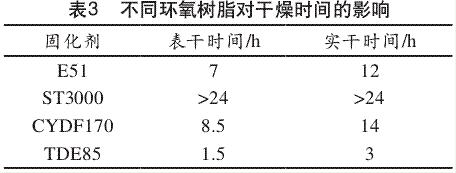
2.2 硬度
涂膜硬度是用户和涂料生产供应商最为关心的性能指标之一,也是海洋船舶涂料的一个最重要的物理性能[7],反映了一个材料抵抗另一个材料压陷、刮擦、切划和渗透的能力。对于本文所考察的4种环氧树脂,固化后的树脂硬度如图2所示。E51、CYDF-170和ST-3000的硬度都在80邵D左右,这是因为它们均为双酚型环氧树脂,分子链上带有的羟基基团可以大大提高分子间作用力,相应的内聚能也较大,从而使得固化树脂的硬度也较高。但当环氧树脂为TDE-85时,由于分子链上没有苯环刚性结构基团,并且分子间作用力相对较小,因而硬度较双酚型环氧树脂低,仅为43邵D。
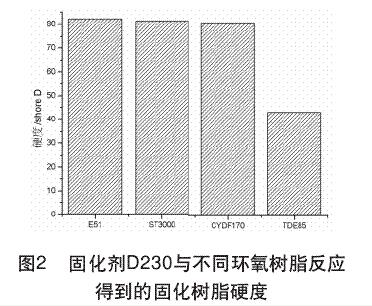
2.3 附着力
对于海洋船用涂料来说,防腐性能是一个重要的考察指标,而高分子涂层充分发挥防腐功能的先决条件在于与金属之间的粘接即附着力的好坏[8]。因此,本文对四种不同结构的环氧树脂固化后的涂层附着力进行了研究,结果如图3所示。对于氢化双酚A环氧树脂ST3000的附着力最大,为4.7MPa,双酚A型环氧树脂E51与双酚F型环氧树脂CYDF170次之,约为4MPa,而混合型环氧树脂TDE85的附着力仅为2.5MPa。涂层在金属底材上附着时,需要有化学活性附着中心[9]。极性基团,特别是羟基和羧基,就能形成这样的化学活性附着中心[10]。由图1可知,双酚型环氧树脂和混合型环氧树脂都带有一定量的极性基团,但是TDE85的固化速度非常快,随着固化交联反应的进行,分子链运动越来越困难,无法扩散移动至钢板表面,极性基团无法与钢板表面发生作用,有效附着的极性基团少,因此附着力很低。而氢化双酚A环氧树脂固化速度最慢,分子链有足够的时间运动至钢板表面,有效附着极性基团最多,附着力最大。
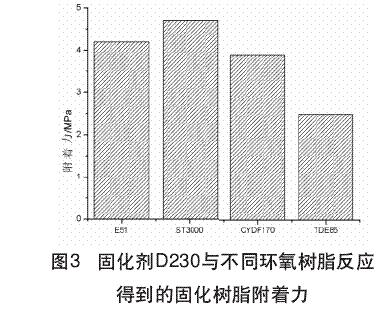