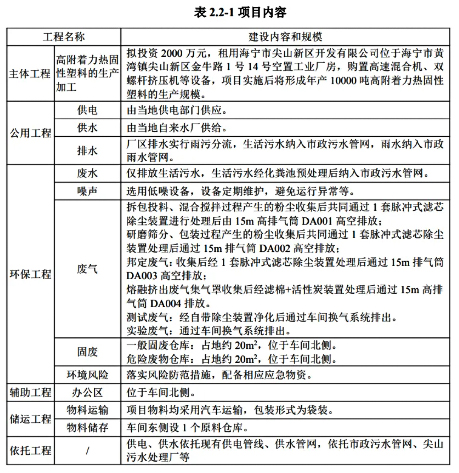
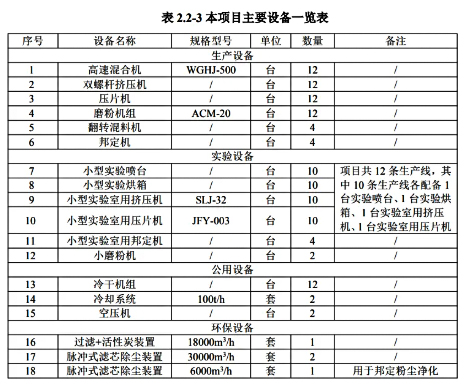
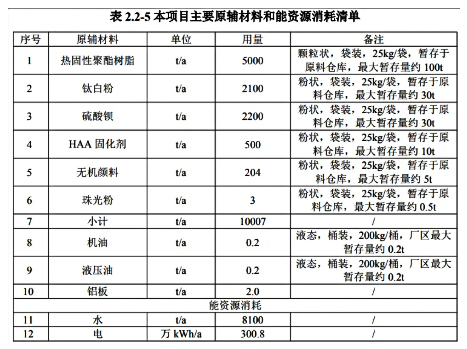
根据上表,本项目主要资源消耗为水资源、电能,用水由当地自来水部门供给; 用电能由当地变电所提供;本项目不新增用地,不会突破地区能源、水、土地等能资 源消耗上线,符合资源利用上线的要求。
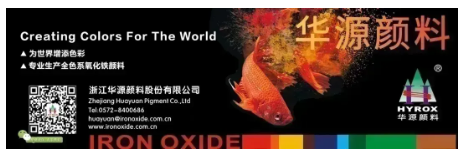
生产工艺简要说明:
(1)称量 按照一定的配比,在配料区将外购的热固性聚酯树脂、硫酸钡、钛白粉、固化剂、 颜料等原料进行称量,批量生产情况下,大宗物料称量时原辅料均未拆包,为袋装称量,仅部分小料需要先拆包后进行称量,因此,该过程基本无粉尘产生。
(2)拆包、投料称重后的各原料拆包后通过人工投料方式倒入高速混合机中,具体操作方式为:将热固性聚酯树脂、硫酸钡、钛白粉、固化剂、颜料等原料提升至高速混合机上方,打开包装袋下料口,粉料在重力作用下落到高速混合机内,投料过程会产生投料粉尘,原料投料后会有部分废包装物产生。
(3)混合搅拌 各原料在密闭的高速混合机或翻转混料机中进行混合搅拌,使各物料充分混合均匀。高速混合机、翻转混料机为密闭设备,混料完成后,开启出料阀门,通过自动控 制装置计量后按一定流量由密闭管道重力输送至挤出机。此过程为完全密闭操作,仅开盖过程有少量粉尘产生。
(4)熔融挤出:混合均匀后的物料混合机内通过重力作用由密闭管道流入双螺杆挤压机加料口,物料从双螺杆挤压机的加料口进入挤压机机筒,机筒第一段为加料段,物料在此阶段不会熔融,随螺杆传动;物料被带入第二段—压缩段,该段为加热段,料斗中混合好 的物料采用电加热棒进行加热,经过 100~120℃左右加温,物料从固态开始熔融,物料间的摩擦力增加,形成高粘体,继续随螺杆传动进入第三段—均化段,达到高聚物 物料彻底均匀地塑化的目的。在此过程中,因为物料软化点温度均小于分解温度,物 料不会进行分解。过程中需将熔融挤出的高温胶状物料进行冷却。
基本原理是:胶状 物料从压出及螺筒内被同向旋转的双螺杆推出后流到双向旋转的循环水冷却滚筒,滚 筒内有不断循环的冷却水,滚筒通过双向紧密挤压将胶状物料碾压成整片状并挤出冷 却。熔融挤出过程中会产生有机废气。
(5)压片冷却: 挤出后物料经过压片机相向转动的压辊得到厚度约 0.5mm 左右的均匀薄状物, 通过不锈钢履带冷却至常温。
(6)研磨筛分:物料压片冷却成型后进入研磨筛分工序,研磨筛分由磨粉机组进行处理,磨粉机 组为密闭设备。片料由喂料电机带动喂料螺杆送入料口,经分布在磨盘外缘碎屑随磨 盘作高速圆圈运动,同时,高速旋转的磨盘使得由均风区进入均风环的风也作高速旋 转,形成强旋风,两者都作用于片料,使片料与片料、片料与磨环、片料与碎屑之间强烈碰撞、剪切摩擦和粉碎研磨,由此生成的粉粒穿过回流圈,沿腔体内壁送入风筛 筛分。风筛筛分主要通过旋风分离器(密闭)将物料进行筛分,研磨粉碎后的物料收 入旋风分离器中,在旋风分离器(密闭)的作用下将粗粉收入粗粉箱内返回磨粉工序重新加工,分离出的超细粉在风机作用下被收集至脉冲除尘器中,将粒度适中的粉末收入成品储藏箱中即为成品。超细粉通过脉冲除尘器进行处理,此过程产生筛分粉尘。
(7)邦定混合:本项目约150t产品需使用邦定机与珠光粉混合,具体操作为:将粉末涂料加入到具有控温夹套的邦定机中,利用邦定机的高速旋转产生摩擦热(温度约 50℃),使粉末涂料颗粒软化,然后迅速将珠光粉加入到高速旋转的粉体中,通过高速旋转的桨叶使珠光粉与软化的底粉颗粒碰撞、摩擦,促使珠光粉嵌入或粘附到底粉表面,投料及出料过程有粉尘产生。
(8)测试:经过研磨粉碎、风筛筛分后的产品即为成品高附着力塑料。本项目共配备10台小型实验喷台、10台小型实验烘箱,在刚生产的成品储藏箱内取一勺产品(每批粉 末开始第一箱必须取样试验,5~6箱取样一次,最后一箱必须取样试验,单条生产线 抽样试验量约10kg/a,12条生产线共0.12t/a),在实验喷台使用喷枪对铝板进行喷涂,然后将喷涂后的铝板送入实验烘箱中进行粉末固化(电加热,烘箱温度200℃,10min),固化结束后及时将铝板取出,自然冷却至室温。通过肉眼观察后,再经过 涂抹厚度检测、硬度监测、色差监测、筛余物监测、粒度分布检测等,若产品经试验 后达不到所需要求,立即停止生产,物料返回进行重新生产。此过程产生喷粉粉尘,粉末固化有机废气、废铝板。
(9)包装入库:成品经磨粉机磨碎后经设备自带的自动称量系统称量后包装,装过程有少量包装粉尘产生。试验合格产品包装入库待售。 此外,每批次产品正式生产前,为确保产品质量,满足客户要求,会在实验室使用实验室用挤出机、压片机、小磨粉机等实验设备进行试制(本项目共配备10台实验室用挤压机、10台实验室用压片机),确保满足客户需求后正式投入生产,实验过程有粉尘以及有机废气产生。
据公开消息显示:嘉兴睿智新材料有限公司由广东睿智环保科技股份有限公司和嘉兴安宇环保科技有限公司于2024年9月份合资成立,广东睿智环保科技股份有限公司持股51%。